Introduction to the HACCP
Brief Explanation of HACCP and Its Importance in Food Safety
Hazard Analysis and Critical Control Points (HACCP) is a globally recognized food safety management system designed to identify, assess, and control hazards in food production. It ensures that potential risks—such as physical, chemical, and biological contaminants—are minimized or eliminated before products reach consumers. Implementing HACCP is crucial for food manufacturers to maintain safety, meet regulatory requirements, and protect their brand reputation.
Among the key hazards addressed by HACCP, physical contaminants like metal, glass, bone, and plastic pose significant risks to consumer health. To effectively mitigate these dangers, food processors must integrate reliable inspection technologies, such as X-Ray inspection machines, into their HACCP programs.
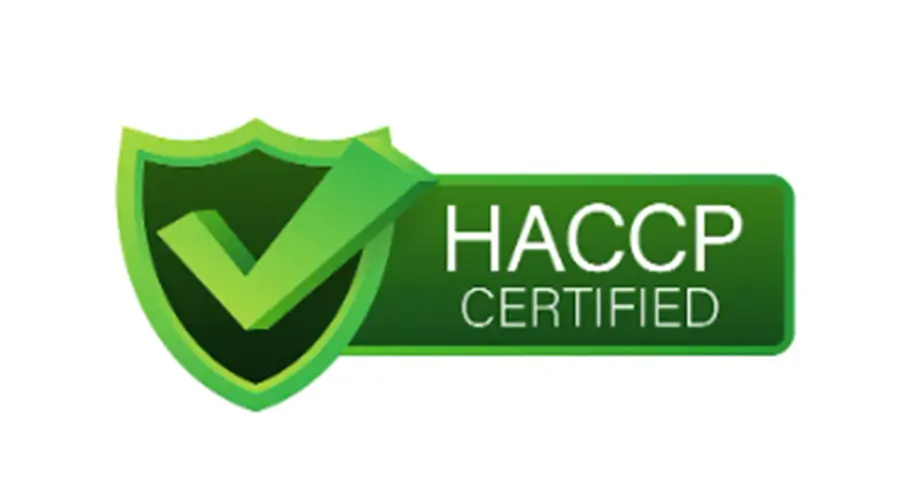
The Growing Need for Advanced Detection Technologies in Food Processing
With increasing regulatory standards and rising consumer expectations, food manufacturers must adopt more advanced solutions to ensure product safety. Traditional inspection methods, such as metal detectors, are limited in their ability to detect non-metallic contaminants, such as glass, bones, and dense plastics. This gap has driven the need for X-Ray inspection for the food industry, which offers superior contaminant detection across a wide range of materials.
X-Ray food inspection systems provide a comprehensive solution for identifying foreign objects, ensuring product integrity, and reducing food waste. These systems are now essential in modern food production, helping companies maintain strict quality control while meeting international food safety standards such as HACCP, FDA, and BRC.
Introduction to X-Ray Inspection Systems as a Key Tool for HACCP Compliance
To effectively manage food safety risks, X-Ray inspection machines have become a crucial component of HACCP-compliant food processing facilities. These advanced systems detect contaminants that other methods might miss, offering real-time monitoring and automated rejection of defective products.
A food X-Ray machine functions by analyzing the density differences between food products and potential contaminants. Unlike traditional inspection tools, X-Ray machines for food inspection can detect a wide range of foreign objects regardless of their composition. This makes X-Ray food inspection systems particularly valuable in industries such as meat processing, seafood production, dairy, and baked goods.
By integrating X-Ray inspection systems into their HACCP framework, food manufacturers can: Improve detection accuracy for physical hazards.
Reduce the risk of contamination-related recalls.
Ensure compliance with global food safety regulations.
Enhance operational efficiency through automated inspections.
In today’s highly regulated food industry, X-Ray inspection for the food industry is not just an option but a necessity for ensuring product safety and maintaining consumer trust. Investing in food X-Ray inspection technology is a proactive step toward achieving HACCP compliance and safeguarding food quality.
Understanding HACCP and Its Critical Control Points (CCPs)
Overview of HACCP Principles and Their Application in Food Processing
HACCP consists of seven key principles designed to manage food safety hazards:
Conduct a hazard analysis
Identify critical control points (CCPs)
Establish critical limits for each CCP
Implement monitoring procedures
Establish corrective actions
Verify the effectiveness of the HACCP system
Maintain documentation and records
The Role of CCPs in Identifying and Controlling Food Safety Hazards
CCPs are essential checkpoints in food production where hazards must be controlled to prevent contamination. A X-Ray inspection system acts as a critical control point by detecting foreign objects and ensuring product integrity. Integrating food X-Ray machines into HACCP programs strengthens food safety efforts and minimizes risks.
Common Contaminants and Defects That Pose Risks in Food Production
Foreign contaminants such as metal, glass, ceramic, stone, dense plastics, and bone fragments can enter the food supply during processing. Additionally, defects such as missing components in packaged food or broken products can impact quality. X-Ray food inspection systems effectively identify and remove these contaminants, preventing unsafe products from reaching consumers.
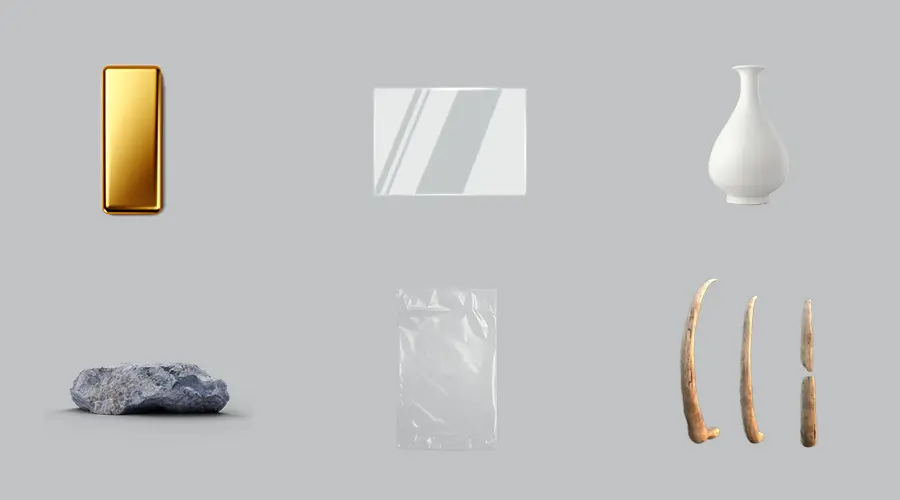
How X-Ray Inspection Systems Support HACCP Compliance
Hazard Detection and Contaminant Removal
X-Ray inspection machines provide advanced detection capabilities, identifying contaminants regardless of their size, shape, or density. Unlike metal detectors, X-Ray machines for food inspection can detect non-metallic foreign bodies such as glass and bone, making them an indispensable tool in HACCP programs.
Monitoring and Verification
Continuous monitoring is a crucial aspect of HACCP compliance. Food X-Ray inspection systems ensure real-time monitoring of production lines, automatically identifying and rejecting contaminated products. This enhances food safety while reducing the burden of manual inspections.
Traceability and Documentation
HACCP requires detailed record-keeping for verification and compliance. X-Ray food inspection systems provide digital logs of inspection results, enabling manufacturers to track and document their quality control processes. This improves traceability and helps businesses meet regulatory requirements such as FDA, BRC, and GFSI standards.
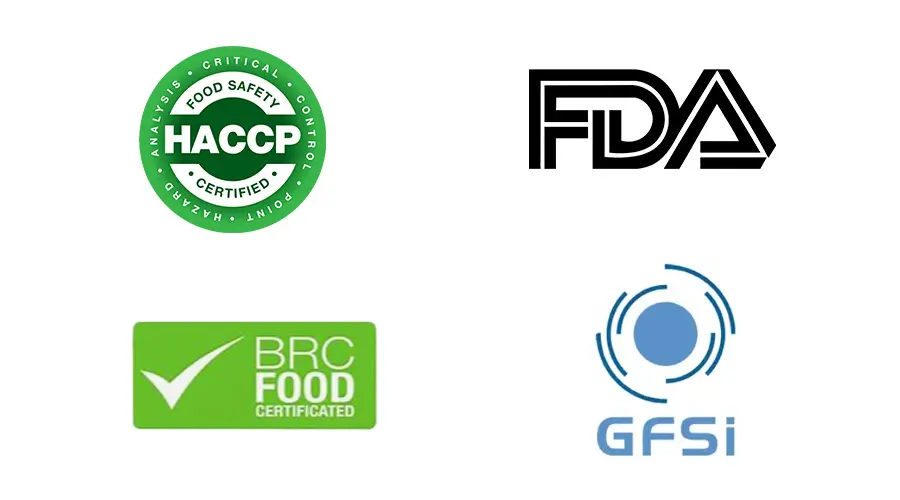
Key Features of X-Ray Inspection Systems for HACCP Compliance
Dual-Energy X-Ray Technology: Enhanced Detection of Low-Density Contaminants
Advanced X-Ray inspection machines utilize dual-energy technology to distinguish between different materials based on their density. This enhances the ability to detect low-density contaminants such as plastic and rubber, which are often missed by traditional detection methods.
Automated Detection Algorithms: Reducing Human Error in Inspections
Modern X-Ray food inspection systems incorporate AI-powered algorithms that automatically identify foreign objects, reducing the reliance on human operators and minimizing the risk of error. These systems improve consistency and accuracy in contamination detection.
Integration with Production Lines: Ensuring Seamless and Efficient Operation
To maintain high efficiency, X-Ray inspection for the food industry is designed for seamless integration with existing production lines. Automated rejection mechanisms ensure that contaminated products are removed without slowing down production, improving operational efficiency.
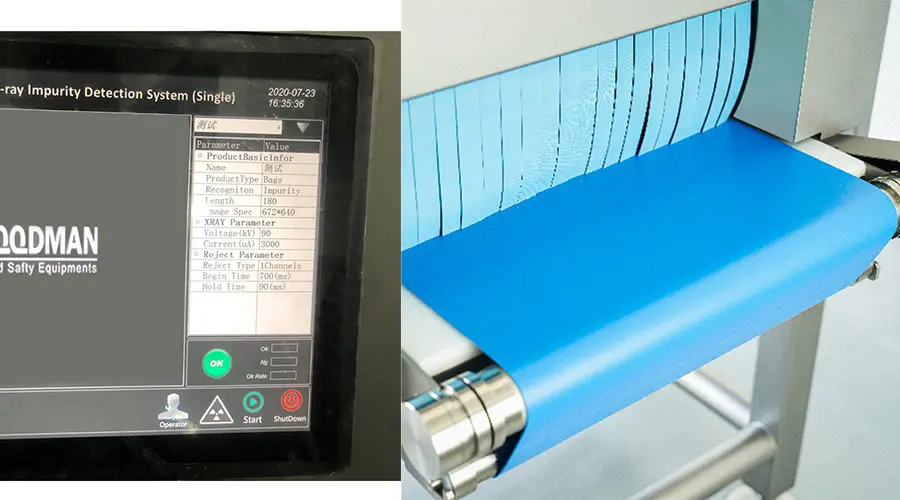
Compliance with Food Safety Regulations: Meeting International Standards
Food manufacturers must comply with global food safety regulations, including HACCP, FDA, BRC, and GFSI. Food X-Ray machines help businesses meet these standards by providing reliable detection capabilities and maintaining detailed compliance records.
Benefits of Using X-Ray Inspection in HACCP Programs
Improved Food Safety and Quality Assurance
By incorporating X-Ray machines for food inspection, manufacturers can enhance their food safety programs, ensuring that only safe, high-quality products reach consumers.
Reduced Product Recalls and Brand Reputation Protection
Product recalls due to contamination can be costly and damaging to brand reputation. X-Ray food inspection systems help prevent recalls by detecting contaminants early in the production process, reducing financial losses and safeguarding consumer trust.
Cost-Effectiveness in Long-Term Operational Efficiency
Investing in X-Ray inspection machines leads to long-term savings by reducing product waste, minimizing downtime, and preventing regulatory fines. Automated inspection also reduces labor costs associated with manual checks.
Increased Consumer Confidence in Food Products
Consumers demand safe and high-quality food products. Food X-Ray inspection reassures consumers that products are free from physical contaminants, strengthening brand loyalty and trust.
Case Studies: X-Ray Systems in HACCP Implementation
Examples of Food Manufacturers Successfully Integrating X-Ray Inspection
Many global food manufacturers have successfully implemented X-Ray inspection systems as part of their HACCP programs. These companies have reported significant improvements in contamination detection, waste reduction, and compliance with food safety regulations.
Real-World Improvements in Contamination Detection and Waste Reduction
A leading dairy manufacturer integrated food X-Ray machines into its HACCP plan and reduced contamination-related product recalls by 90%. Another meat processing company detected and removed bone fragments more effectively using X-Ray food inspection systems, improving product quality and safety.
Conclusion
Recap of Why X-Ray Inspection is Essential for HACCP Compliance
X-Ray inspection for the food industry plays a vital role in HACCP compliance by detecting contaminants, monitoring critical control points, and ensuring product traceability. Integrating food X-Ray inspection into quality control processes is crucial for maintaining food safety and regulatory compliance.
The Future of Food Safety Technology and Innovations in X-Ray Detection
As technology advances, X-Ray food inspection systems will become even more intelligent and efficient. AI-driven enhancements, IoT connectivity, and automation will further improve contamination detection and streamline food safety processes.
Invest in X-Ray Inspection for Enhanced Compliance and Quality Control
Food manufacturers looking to enhance safety and HACCP compliance should invest in X-Ray inspection machines. By adopting food X-Ray inspection technology, businesses can reduce contamination risks, protect their brand reputation, and build consumer trust in their products. For companies committed to food safety excellence, X-Ray inspection for the food industry is not just an option—it‘ s a necessity.