Introduction: The Sustainability Challenge in Manufacturing
Growing Pressure on Manufacturers to Reduce Waste and Environmental Impact
As environmental concerns and regulatory pressures rise, manufacturers across industries are under increasing scrutiny to minimize waste and reduce their carbon footprint. From food production to pharmaceuticals, sustainability is no longer a value-added — it’s a business imperative. In response, many companies are turning to advanced X-Ray inspection equipment as a powerful tool to support eco-conscious operations. These systems, once solely focused on product safety, now contribute directly to environmental goals by reducing material waste and improving production efficiency.
Balancing Quality Control with Eco-Conscious Production Goals
One of the greatest challenges for sustainable manufacturing is maintaining rigorous quality control while also minimizing resource consumption. Traditional inspection methods often result in excessive waste — through unnecessary rejections, batch recalls, or destructive testing. However, modern X-ray inspection machines offer a smarter, greener alternative.
In particular, food X-Ray inspection systems are transforming how producers detect contaminants, verify packaging integrity, and ensure proper fill levels — all without destroying the product or the packaging. These machines help reduce food waste, conserve resources, and streamline compliance with safety regulations.
Introduction to X-Ray Inspection as a Green Tech Solution
Today’s X-Ray inspection machines are engineered not only for precision but also for sustainability. By detecting defects in real-time and isolating only the problematic units, they prevent mass discards and enable leaner operations. Whether you’re inspecting packaged meals, pharmaceuticals, or cosmetics, X-Ray inspection equipment supports green manufacturing without compromising on safety, compliance, or performance.
X-Ray Inspection and Waste Reduction: The Connection
Early Detection of Defects Prevents Full-Batch Discards
In traditional production environments, when defects go unnoticed until later stages—or worse, reach the end customer—entire batches may be discarded. This leads to significant material and financial loss. Modern X-Ray inspection equipment changes that by enabling early-stage, inline detection of foreign objects, seal failures, or fill-level anomalies.
By identifying these issues in real-time, manufacturers can isolate and remove the specific faulty products before they move further along the supply chain. This early intervention not only saves usable products but also prevents unnecessary full-batch recalls.
Non-Destructive Testing Means No Product Loss During Inspection
Unlike some forms of destructive sampling and manual inspection, X-Ray inspection machines allow for non-destructive testing. This means that every product can be inspected—without being damaged or opened—preserving its commercial value and reducing product loss during quality control.
For example, in food X-Ray inspection, items like vacuum-packed meats or bottled beverages can be examined for bones, metal shards, or glass fragments without compromising the packaging. This ensures both safety and sustainability.
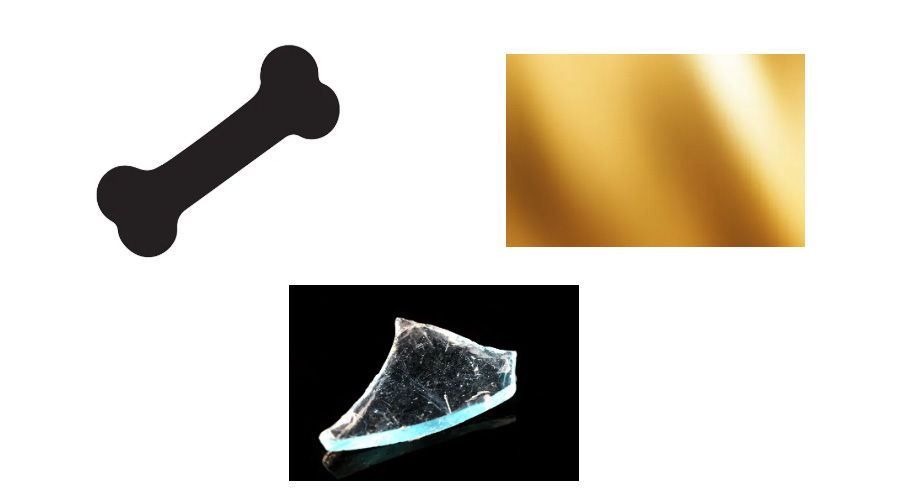
Accurate Rejection of Only Faulty Items—No Unnecessary Waste
One of the most important features of advanced X-Ray inspection systems is their precision. Integrated with AI algorithms and high-resolution imaging, these machines can accurately differentiate between acceptable variances and true defects. This minimizes false rejects, a common issue that leads to unnecessary waste of good products.
Instead of removing large quantities of items out of caution, X-Ray systems allow only non-compliant units to be automatically rejected. This targeted rejection process keeps waste levels low, maintains throughput, and boosts overall resource efficiency—making it a vital part of any green production strategy.
Minimizing Material Waste in Packaging
Verifying Fill Levels Reduces Overpackaging
Overpackaging is one of the most common causes of material waste in food and pharmaceutical industries. When a product is overfilled, it not only leads to excess usage of primary materials but can also compromise packaging integrity. With X-Ray inspection equipment, manufacturers can accurately verify the fill levels of liquids, powders, and solids—ensuring consistency without unnecessary overuse of materials.
In food X-Ray inspection, for example, fill-level analysis helps companies meet regulatory requirements while reducing raw material costs. By maintaining optimal fill levels, brands can eliminate packaging waste and create more sustainable production practices.
Seal Integrity Checks Prevent Leaks and Rework
Faulty seals lead to leaks, contamination, and the need for costly rework or disposal. Traditional inspection methods often miss micro-seal failures, but X-Ray inspection machines equipped with high-resolution imaging and AI algorithms can detect even the smallest seal imperfections in real time.
This level of quality control prevents defective items from continuing down the production line, reducing wasted packaging, rejected shipments, and resource-intensive reprocessing. It also ensures that packaging performs its intended function—protecting the product from contamination and spoilage.
Ensuring Proper Component Presence Avoids Incomplete Shipments
Incomplete or improperly assembled products can result in returned goods, consumer dissatisfaction, and wasted packaging. X-Ray inspection machines can verify the presence and positioning of internal components—such as desiccants, caps, blister items, or secondary packaging elements—without opening or damaging the product.
In sectors like food X-Ray inspection and medical packaging, this capability ensures that every unit leaving the factory is complete and compliant, avoiding the downstream waste and cost associated with incomplete shipments.
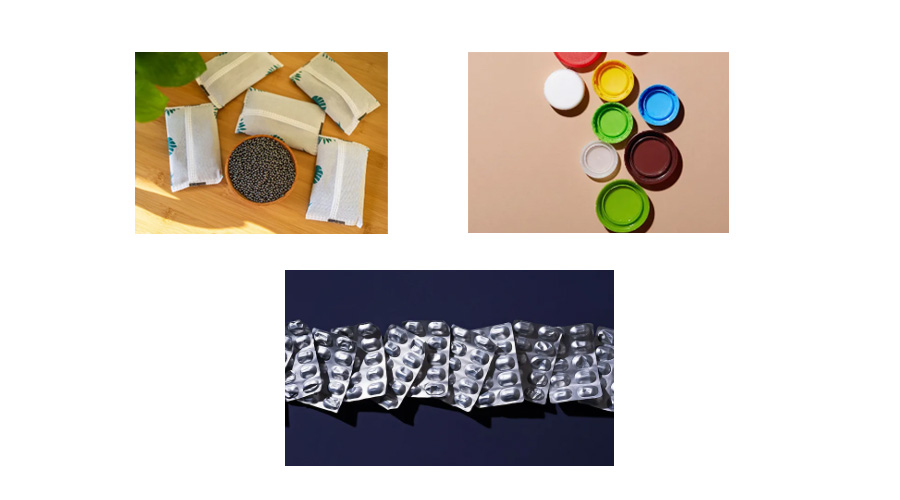
Enhancing Production Efficiency with AI
AI-Driven Defect Detection Optimizes Accuracy
Artificial intelligence is revolutionizing modern quality control by dramatically improving the accuracy of defect detection in manufacturing lines. Today’s X-Ray inspection machines are equipped with AI algorithms trained to identify even the most subtle anomalies—whether it’s a hairline crack in packaging, an underfilled product, or an unexpected foreign object.
In the realm of food X-Ray inspection, AI-powered systems can distinguish between acceptable product variations and actual contaminants with remarkable precision. This minimizes human error and ensures that only defective items are flagged, helping manufacturers maintain high standards without slowing down operations.
Fewer False Rejects = Less Wasted Good Product
Traditional inspection methods, and even some early X-ray systems, often produced high false reject rates—leading to the disposal of perfectly good products. Modern X-Ray inspection equipment, powered by deep learning and pattern recognition, significantly reduces these false positives.
By precisely identifying real defects while passing compliant items, manufacturers reduce unnecessary waste, increase yield, and maximize efficiency. This is especially critical in industries like food and pharma, where every gram of raw material counts and waste reduction is a top priority.
Data Analytics Help Identify Process Inefficiencies Early
Advanced X-Ray inspection machines do more than just detect defects—they collect data. When paired with analytics tools, this inspection data provides valuable insights into production trends, recurring issues, and potential equipment failures.
By identifying patterns in real time, manufacturers can proactively address inefficiencies—such as a misaligned filling nozzle or faulty sealing equipment—before they result in large-scale product loss. In this way, X-Ray inspection equipment not only acts as a gatekeeper for quality control, but also as a powerful tool for continuous improvement and sustainable production management.
Case Study: Greener Operations Through X-Ray Integration
Example: A Food or Pharma Company Reducing Packaging Waste
To better illustrate the environmental and operational benefits of X-Ray inspection equipment, let’s look at a real-world case from a mid-sized food manufacturing company. Facing increasing pressure from both regulators and sustainability-conscious customers, the company set a goal to reduce packaging waste without compromising on product quality control.
They integrated a state-of-the-art food X-Ray inspection system equipped with AI-powered imaging and automatic reject functionality. The X-Ray machine was positioned after the packaging line to inspect each item for underfills, broken seals, and foreign materials such as metal or plastic.
Results: 38% Reduction in Scrap, 25% Improved Resource Use
Within three months of implementation, the company reported a 38% reduction in packaging scrap, as the X-Ray system caught defects early—before entire product batches had to be discarded. The real-time inspection also helped adjust upstream processes, like correcting a filling inconsistency that had previously gone undetected.
Material use became more efficient, with a 25% improvement in resource utilization, since fewer perfectly good products were being rejected due to manual inspection error. Most importantly, the integrity of packaging was ensured—critical for consumer trust and shelf-life stability.
ROI in Both Cost Savings and Environmental Footprint
From a business perspective, the return on investment was clear. The reduction in product loss, labor costs for manual re-inspection, and improved production speed led to noticeable financial savings within the first year. Environmentally, the shift meant fewer materials ended up in landfills, helping the company align with its corporate social responsibility (CSR) and ESG goals.
This case proves how X-Ray inspection machines are not only a solution for quality control, but also a smart investment in sustainability. With the right configuration and training, these systems can drive measurable improvements in both cost and environmental impact.
Compliance with Green Manufacturing Standards
Aligning with ISO 14001, ESG Goals, and CSR Initiatives
Modern manufacturers are under increasing pressure to not only maintain high quality control standards, but also to align with environmental and social frameworks such as ISO 14001, ESG (Environmental, Social, and Governance) goals, and broader CSR (Corporate Social Responsibility) strategies. Implementing X-Ray inspection equipment is one effective way to meet these goals.
For example, food X-Ray inspection systems help minimize waste by accurately identifying only defective products, reducing the volume of unnecessary rework or discarded batches. This aligns with ISO 14001’s principles of minimizing environmental impact through optimized processes. Additionally, the use of energy-efficient X-Ray inspection machines supports ESG benchmarks for sustainable operations and resource efficiency.
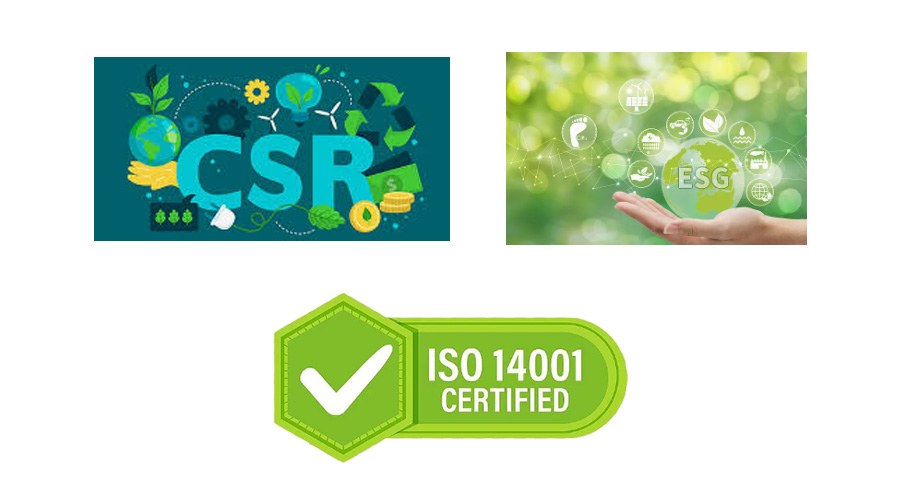
Digital Traceability for Better Reporting and Transparency
Green manufacturing is not just about doing better — it’s also about proving it. Today’s X-Ray inspection equipment comes with integrated data logging and traceability features, allowing manufacturers to maintain detailed inspection records and generate audit-ready reports. These capabilities support compliance with sustainability certifications and make it easier to report progress toward environmental goals.
In regulated industries such as food and pharmaceuticals, traceability is essential not only for quality control, but also for accountability in the case of recalls or audits. Digital traceability ensures that every inspected item — whether it passes or fails — is documented and traceable through the supply chain.
Supporting Circular Economy Principles
One of the core ideas of green manufacturing is the shift toward a circular economy — where products, packaging, and materials are kept in use for as long as possible. X-Ray inspection machines contribute to this by reducing waste and helping ensure that only defective items are removed, enabling the rest of the batch to be reused or redistributed.
In food production, for instance, detecting a broken seal or missing component early in the line allows manufacturers to salvage or repurpose materials that would otherwise be discarded. This significantly reduces raw material consumption and supports circular practices, especially when paired with sustainable packaging materials.
Long-Term Environmental and Business Benefits
Reduced Landfill Contributions
One of the most tangible long-term environmental advantages of integrating X-Ray inspection equipment into production lines is the significant reduction in landfill contributions. By enabling early and precise defect detection, manufacturers can isolate and remove only the faulty products rather than discarding entire batches. This targeted approach drastically cuts down on overall product waste — especially in industries like food X-Ray inspection, where even minor contamination can traditionally result in mass disposal.
As manufacturers shift toward sustainable practices, X-Ray inspection machines provide a non-destructive, environmentally friendly way to maintain high standards while minimizing ecological impact. Fewer rejected batches mean fewer perfectly usable materials end up in landfills.
Lower Resource Consumption and Energy Use
Beyond waste reduction, X-Ray inspection systems help optimize resource consumption across production cycles. Precise quality control reduces the need for reprocessing, rework, and additional raw material use, all of which contribute to energy savings and improved operational efficiency.
For example, in food production environments, detecting underfilled or improperly sealed packages in real time avoids unnecessary repackaging and prevents downstream waste. Over time, this not only conserves raw materials but also reduces the energy required to manufacture replacement goods — resulting in a lighter carbon footprint.
Enhanced Brand Reputation Among Eco-Conscious Consumers
Modern consumers are increasingly eco-aware and demand accountability from the brands they support. Companies that adopt sustainable inspection technologies, such as X-Ray inspection equipment, send a clear message about their commitment to environmental responsibility.
Publicizing the use of intelligent X-Ray inspection machines as part of a broader green manufacturing initiative can enhance brand image, build consumer trust, and create differentiation in competitive markets. For industries like food and pharma, where product integrity and environmental stewardship are both mission-critical, such technologies deliver a win-win — safer products and a cleaner planet.
Conclusion: Smarter, Greener Quality Control with X-Ray
Recap of X-Ray’s Role in Sustainable Manufacturing
As industries around the world strive for greener, more efficient production practices, X-Ray inspection equipment has emerged as a vital tool in achieving both environmental and operational goals. From reducing waste and minimizing packaging errors to optimizing raw material usage, these systems offer a comprehensive solution for sustainable quality control.
In sectors such as food X-Ray inspection, where safety and consistency are paramount, the ability to detect foreign bodies, verify seal integrity, and monitor fill levels—without destroying the product—ensures that only defective items are removed. This precision helps manufacturers significantly reduce unnecessary waste and lower their overall environmental footprint, while maintaining strict compliance with regulatory standards.
Future Outlook: AI + IoT for Even Greater Eco-Efficiency
Looking ahead, the integration of AI and IoT technologies into X-Ray inspection machines is paving the way for even more intelligent and eco-efficient operations. Predictive analytics will enable systems to identify defect trends before they escalate, while real-time data sharing can streamline decisions across connected production lines.
As AI continues to evolve, X-Ray inspection equipment will become even more adept at identifying subtle anomalies, reducing false rejects, and enhancing product traceability. These innovations will not only support circular economy principles but also empower manufacturers to meet increasingly stringent ESG and sustainability goals with confidence.
Upgrade to Intelligent Inspection for a Cleaner Tomorrow
Adopting intelligent, eco-conscious inspection solutions is no longer a choice—it’s a necessity. Manufacturers that upgrade to advanced X-Ray inspection machines position themselves as leaders in both quality assurance and environmental responsibility.
Whether in pharmaceuticals, medical devices, or food X-Ray inspection, investing in smarter quality control technology today helps create a cleaner, safer, and more sustainable future for all.
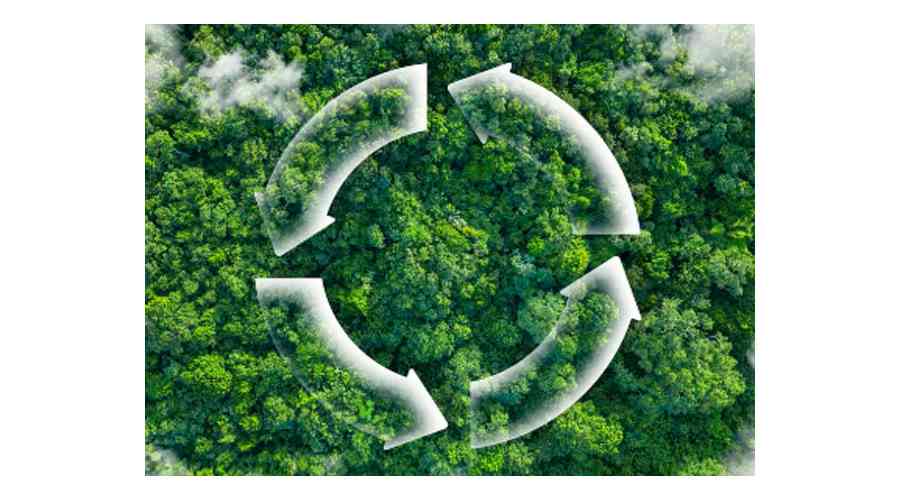