Introduction
As a food processor, you know that x-ray machines are crucial in combating food contaminants in the production line. These systems help protect your brand and ensure customer safety.
Choosing the right food x-ray inspection system is vital for the success of your inspection program and for meeting government regulations and consumer expectations. It’s important to identify the most suitable x-ray machine model for your operations and the optimal placement within your production line.
This article will guide you on how to evaluate and select different types of x-ray inspection systems and where to position them in your processing line. Let’s get started!
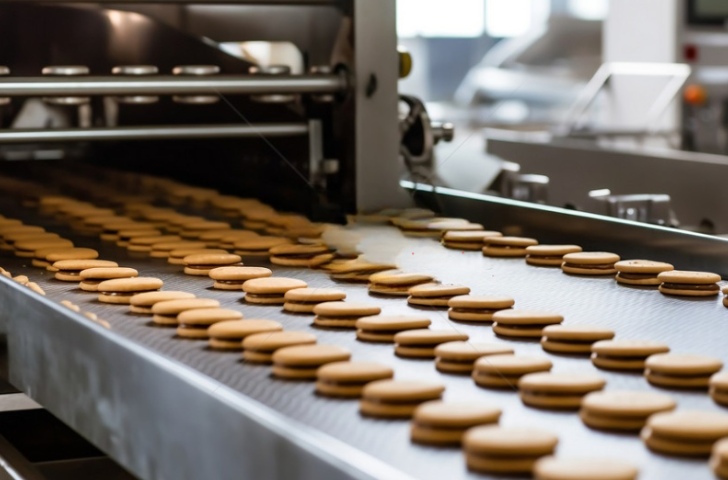
6 Key Points to Choose the Best X-ray Inspection for You
Selecting the right x-ray inspection system is crucial for ensuring food safety in your production line. While many machines share fundamental functionalities, their specific performance characteristics can significantly impact your food safety protocols. Here are six essential principles to guide your selection:
System Compatibility
Evaluate the specific products you plan to inspect, including the type of food, packaging materials, and dimensions. Different products may require distinct inspection capabilities, so it’s vital to choose a system that meets your needs and complies with food safety regulations. This understanding will also help determine the appropriate size and capacity for effective operation.
Versatility and Connectivity
Look for an x-ray system that can adapt to your production line’s evolving requirements. Ensure it integrates smoothly with existing equipment and offers features like data reporting and Ethernet connectivity for real-time monitoring. Ideally, the system should handle both raw material inspections and final product evaluations.
Safety and Cleanliness
Prioritize safety features that protect your brand, employees, and consumers. The system should comply with established radiation safety standards and include robust data security measures. A hygienic design that allows for easy cleaning and maintenance is essential to minimize cross-contamination risks.
Efficient Data Management and Storage
Choose a system capable of storing substantial data to enhance quality assurance processes. Advanced image analysis technologies should enable sensitive detection of foreign objects and accurate product inspections, ultimately improving efficiency and reducing the risk of recalls.
User Operation
Select an intuitive machine that minimizes the chances of human error. Ensure the initial setup is performed by a qualified expert, and that the system features user-friendly electronic controls for easy navigation, enhancing overall efficiency.
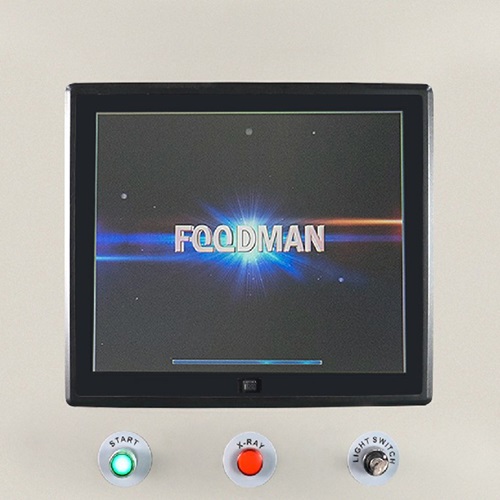
Assistance and Coverage
Choose a manufacturer that provides comprehensive service and support to maintain your x-ray inspection system. Ongoing assistance, a solid warranty, and reliable customer service are crucial for ensuring optimal functionality and providing peace of mind.
By considering these principles, you can make an informed decision when selecting the right x-ray inspection system for your food processing operation. This careful selection will enhance safety and quality in your production line, helping you meet consumer expectations and regulatory compliance.
Tips for Picking the Best X-Ray Inspection System for Your Production Process
Food processors depend on x-ray machines not only to safeguard consumer health but also to maintain their brand reputation in a competitive market. Selecting the appropriate inspection system is crucial for ensuring effective food safety protocols that protect both the manufacturer and the consumer. This guide provides an overview of the different types of x-ray systems available for your production line, helping you make an informed decision based on your specific needs.
X-Ray Inspection System for Packaged Goods
Vertical beam x-ray machines are among the most common choices for detecting contaminants in packaged food products. These systems excel in identifying foreign objects due to their design, which utilizes vertical cross-sections that offer optimal sensitivity for smaller packages. The vertical orientation helps in effectively scanning through the minimal depth of many packaged items.
Typically, these x-ray scanners are equipped with a conveyor system that transports packages through the x-ray beam, ensuring a streamlined inspection process. After inspection, the conveyor returns the packages to the production line. Many modern models come with an automatic rejection mechanism, which efficiently removes defective packages from the production process, thereby enhancing quality control.
The x-ray generator is usually situated at the top of the machine, directing its beam downward through the products toward a detector. For thorough inspections, it’s essential that each package fits within the triangular-shaped vertical beam and is centrally positioned on the conveyor belt. The size of the x-ray beam must be adjusted according to the maximum dimensions of the packages being inspected to ensure effective scanning.

X-Ray Inspection System for Fish Bone
The X-Ray Inspection System for Fishbone is a precision tool tailored to detect small fishbones in fish meat, offering high accuracy and speed to boost product safety and quality for fish processors. Suitable for a range of products, including fillets, whole fish, and processed fish, this system improves efficiency and adapts to various production setups, all while meeting rigorous safety standards.
Equipped with ultra-high-resolution imaging and TDI (Time Delay Integration) technology, the system captures detailed images that enable accurate detection of even the smallest fishbones. FIAP image processing technology further optimizes detection, ensuring thorough inspection by identifying bones that may otherwise be overlooked. An external high-definition display and a segmented protective cabin effectively reduce radiation and secondary contamination, contributing to a safe operating environment.
A streamlined user interface includes the latest Windows operating system, a 50-inch 4K display, and a 17-inch full-color touch screen for enhanced visibility and ease of operation. The interface also features built-in data backup to prevent loss and ensure smooth operation.

Dual Enery X-Ray Inspection System for Bones
Detecting small, hard, and calcified bones in poultry processing is challenging due to the bones’ low density and irregular shapes. Effective detection is crucial for maintaining high safety standards, as traditional methods often struggle with these issues.
The Dual Energy X-ray Inspection System is designed to meet modern poultry industry needs by accurately identifying calcified and small bones in various products, from boneless raw meat like chicken breasts and wings to processed items such as chicken nuggets and sausages. By analyzing density differences, the system’s dual-energy technology can distinguish bone fragments from meat, even when embedded or nearly invisible.
With advanced image processing, this system ensures consistent quality and safety, effectively detecting non-metallic contaminants. It enhances reliability, supports regulatory compliance, reduces waste, and minimizes recall risks—reinforcing brand reputation and safety in production lines. This versatile solution is invaluable for poultry processors committed to delivering safe, quality products to consumers.

What Type of Rejector Is Best for X-Ray Inspection Systems?
Selecting the appropriate rejector system for your x-ray inspection machines involves factors like conveyor belt speed, package dimensions and weight, and the operational environment. Here are some common rejector options:
Air Blast Rejector
Designed for packages up to 850 grams, the air blast rejector is effective for small items on narrow conveyor belts. It uses a nozzle to eject rejected packages without disrupting the production flow, making it ideal for closely packaged products like potato chips and granola bars. However, it’s not suitable for open or fragile packages, which may break during rejection.
You can adjust the air blast rejector using a variable airflow valve, with “reject delay” indicating the time from detection to ejection and “reject duration” showing how long the air blast is applied.
Pusher Rejector
The pusher rejector is suitable for heavy, rigidly packaged products. It employs a mounted pusher blade to eject contaminated items into a reject bin, operating from the side or overhead depending on the production line layout. This rejector is not recommended for poly-bagged products, as they may get stuck. A rejector brush strip can help mitigate this risk. Standard side and overhead pushers handle up to 10 kilograms, while heavy-duty versions can accommodate up to 50 kilograms, with a maximum pack rate of 15 packages per minute.
32/64 Lanes Air Blast for Bulk Goods
In bulk-flow applications, the 32/64 air blast rejector enhances rejection accuracy. It captures images across the entire width of the conveyor belt without distinct lanes. The angled nozzles target falling products, delivering an air blast that propels contaminated packages away from the main flow into a designated container.
When choosing a rejector for your x-ray inspection system, consider the types of products and specific needs of your production line. Each rejector type has unique benefits and limitations, so it’s essential to match the rejector to your operational requirements for optimal efficiency.
What is the Optimal Position for Inspection in the Production Line?
X-ray inspection systems provide versatile functionality throughout the production process, prompting manufacturers to strategically install these systems at key control points within the production line to maximize their benefits.
These crucial points for effective x-ray inspection include checking loose or bulk-flow items, evaluating raw materials, and assessing pumped products. Additionally, they can be utilized to inspect products during and prior to processing, review products after processing, and examine items before packaging and sealing. Furthermore, x-ray systems play a vital role in analyzing products after packaging and sealing, as well as inspecting final sealed products.
While x-ray inspection is beneficial at each of these points, the ideal placement of x-ray equipment ultimately depends on the specific needs of the food processor. It is crucial to identify which positions will provide the best results and enhance operational efficiency. Additionally, the selected location should aim to mitigate potential risks.
Conclusion
A reliable food x-ray inspection system is crucial for identifying contaminants, safeguarding consumer health, preserving your business’s reputation, and minimizing costs. Choosing the appropriate system improves efficiency across food processing stages, leading to comprehensive, swift, and dependable inspections. Evaluate the factors outlined in this article to determine the most suitable x-ray food inspection system for your operations.
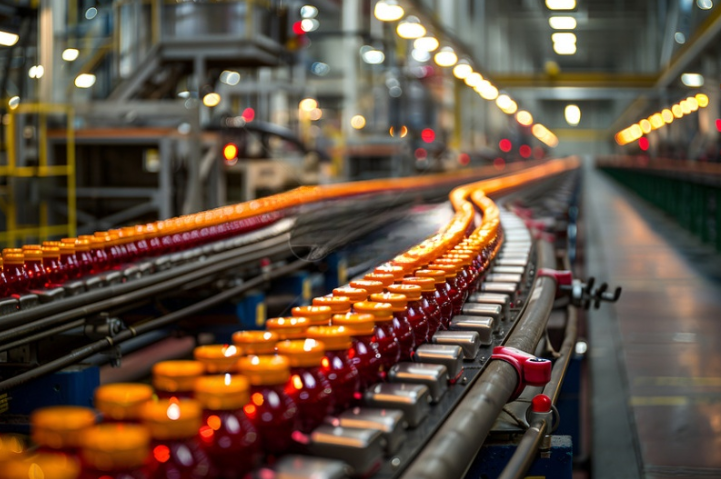