Introduction: The Rising Demand for Defect-Free Bottled Products
In today’s competitive beverage and pharmaceutical industries, ensuring product quality is more critical than ever. A vision inspection system plays a vital role in maintaining the integrity of bottled products, eliminating defects, and ensuring compliance with industry regulations. By integrating advanced vision systems for inspection, manufacturers can detect and reject defective bottles in real-time, preventing quality issues before they reach consumers. Whether it’s ensuring label accuracy, detecting cap defects, or identifying surface imperfections, vision system inspection equipment enhances efficiency, reduces human error, and guarantees product consistency.
Why Bottled Product Quality Matters
Consumer Expectations for Flawless Packaging
In the beverage, pharmaceutical, and food industries, consumers associate packaging quality with product reliability. A single mislabeled or damaged bottle can erode trust in a brand.
Industry Compliance and Regulatory Requirements
Strict quality control regulations mandate proper labeling, sealing, and packaging integrity. Non-compliance can result in legal penalties and product recalls.
Impact of Defects on Brand Reputation
Negative customer reviews and recalls due to packaging defects can cause long-term damage to a brand. Ensuring defect-free bottles is essential for maintaining customer loyalty and trust.
Common Bottling Defects and Their Consequences
Even with the most advanced manufacturing processes, defects can occur during high-speed bottling operations. Common issues include:
Misaligned or Missing Labels – Causes compliance issues and confuses consumers.
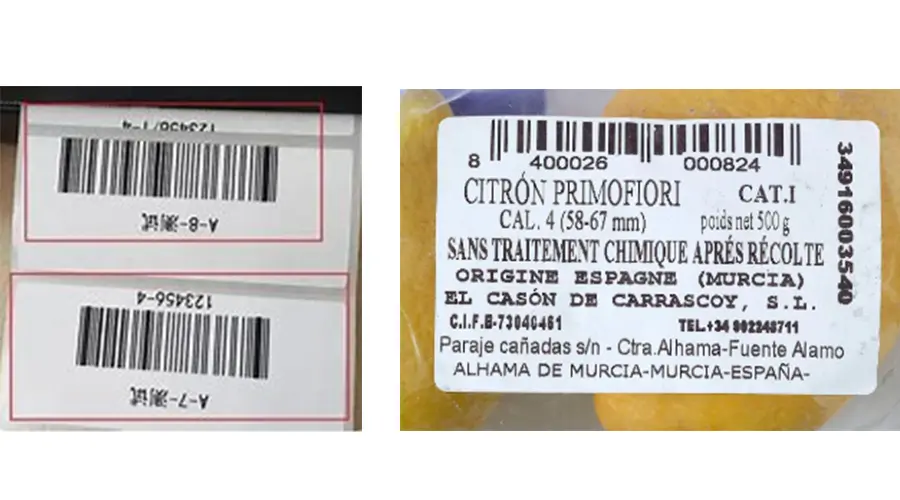
Loose, Broken, or Missing Caps – Leads to leakage and product contamination.
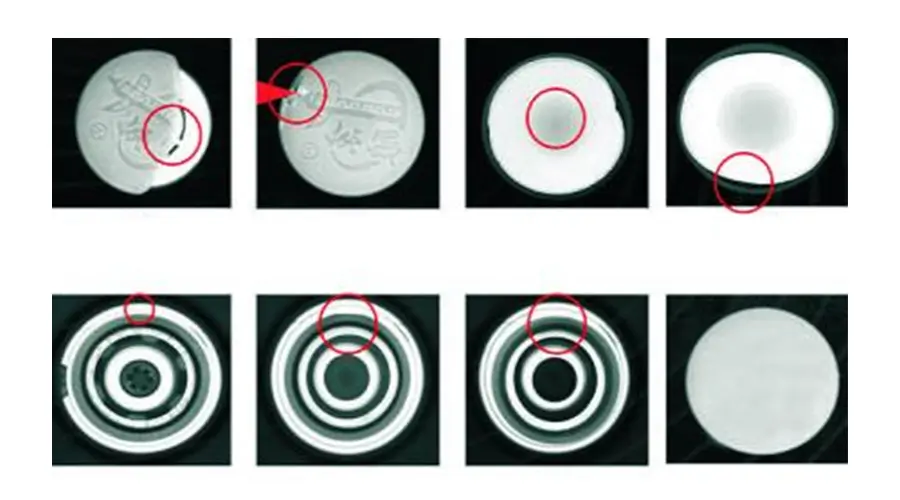
Leaking or Contaminated Products – Results in safety concerns and costly recalls.
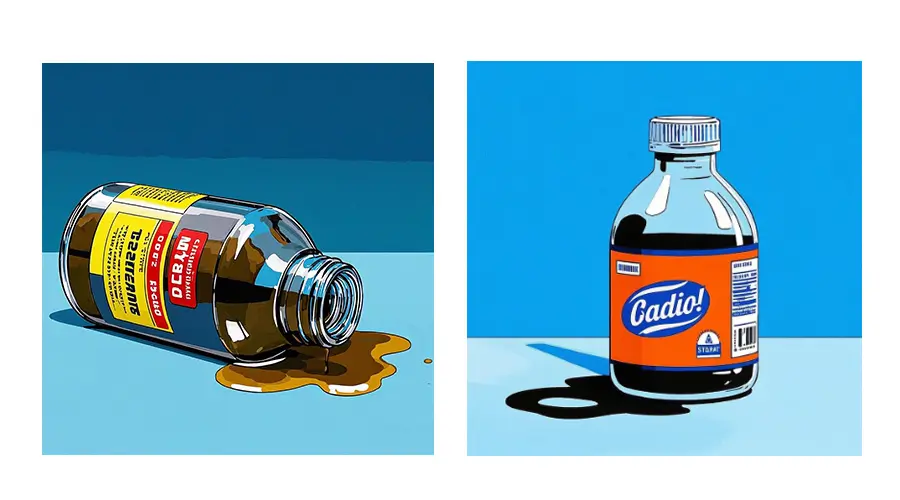
Cracked or Misshapen Bottles – Affects product integrity and transportation durability.
Without a vision inspection system, detecting these defects manually is challenging, leading to quality inconsistencies.
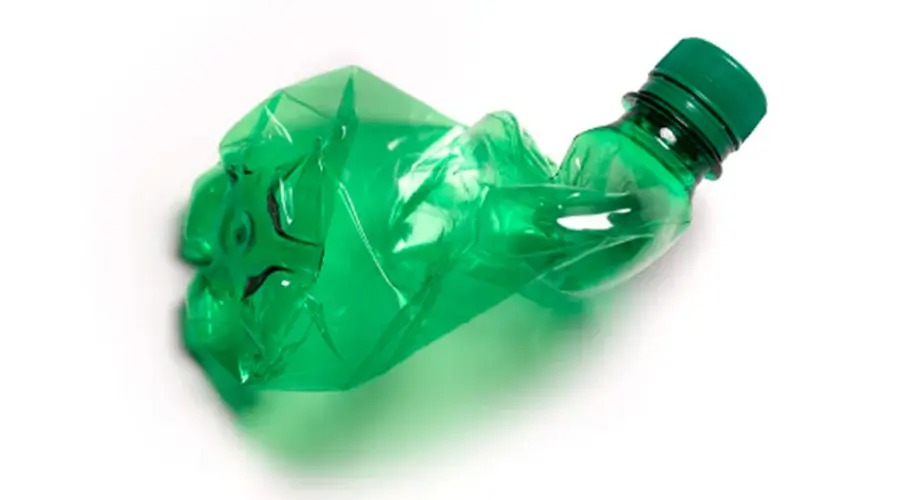
How the Foodman Vision Inspection System Detects Every Defect
High-Speed AI-Powered Label Inspection
A bottle’ s label is its identity, and errors in labeling can cause misbranding and compliance issues. The Foodman Vision Inspection System ensures label accuracy with:
Advanced AI technology that detects skewed, misplaced, or missing labels.
Optical character recognition (OCR) to verify barcodes, QR codes, and expiration dates.
Database integration to ensure printed information matches product specifications.
Cap & Seal Integrity Inspection for Leak Prevention
Improper sealing leads to product spoilage and contamination risks. Foodman’ s AI-powered inspection system guarantees:
Detection of loose, tilted, or missing caps to prevent leaks.
Identification of seal integrity issues, such as weak closures or micro-cracks.
Prevention of foreign object contamination through advanced imaging analysis.
Structural & Surface Defect Detection
A bottle must maintain its shape and integrity throughout distribution. The Foodman Vision Inspection System performs:
High-resolution scanning to detect cracks, dents, or misshapen bottles.
Real-time defect identification to prevent production line issues.
Glass and plastic bottle analysis to maintain durability during storage and transport.
The Role of AI & Automation in Bottling Inspection
How AI Enhances Quality Control
Unlike traditional inspection methods, AI-driven vision inspection improves defect detection over time by learning from data patterns. This results in:
Self-optimizing defect recognition, reducing false rejections.
Instant adjustments to production parameters, improving efficiency.
Consistent quality control without reliance on human operators.
High-Speed Analysis for Maximum Productivity
Foodman’ s vision system operates at high production speeds without slowing down the bottling process. It enables manufacturers to:
Maintain high throughput while ensuring quality.
Detect and remove defective products in real time.
Reduce manual inspection costs and labor-intensive processes.
Reducing Human Errors & Ensuring Consistency
Human inspection is prone to fatigue and inconsistencies, especially in high-speed production. Automated AI-powered inspection systems ensure:
Standardized quality control with no variations.
24/7 operational efficiency without human oversight.
Lower defect rates and higher customer satisfaction.
Key Benefits of Foodman’s Vision Inspection System
Integrating Foodman’s Vision Inspection System into your bottling line provides:
Zero-defect quality assurance through AI-driven precision.
100% inline inspection at high production speeds.
Automatic defect rejection, reducing waste and increasing efficiency.
By minimizing human error and maximizing accuracy, Foodman ensures that every bottle meets the highest quality and safety standards.
Conclusion: The Future of Bottling Quality Control
Why AI-Driven Inspection is the New Industry Standard
The shift towards AI-powered automation is transforming bottling quality control. With advanced deep learning algorithms, real-time defect detection, and high-speed analysis, Foodman’s Vision Inspection System offers manufacturers a reliable, scalable, and cost-effective solution for achieving zero-defect bottled products.
How Foodman Helps Manufacturers Achieve Superior Quality
By implementing Foodman’s progressive vision technology, manufacturers can:
Eliminate packaging and sealing defects.
Enhance production efficiency without compromising quality.
Meet regulatory compliance and prevent costly recalls.
Get a Live Demo or Consultation Today
Don’t let defective products impact your brand reputation. Contact Foodman today for a live demo and see how our Vision Inspection System can revolutionize your bottling quality control.