Introduction
Food recalls are a costly nightmare for any business, affecting both finances and reputation. They not only lead to revenue loss due to wasted products but also damage consumer trust, which is far harder to rebuild. To combat these risks, advanced X-Ray inspection systems have become an essential part of modern food safety strategies. These food X-Ray Inspection machines identify and eliminate contaminants during production, ensuring that only safe, high-quality products reach consumers.
Why Food Recalls Happen
Common Contaminants in the Food Supply Chain
Food contamination can occur at various stages of the supply chain. Production processes may introduce metal fragments, glass shards, stones, plastics, or bones due to equipment wear, broken containers, or raw material impurities. Packaging poses additional risks, such as loose plastic or machine components entering products during sealing, while transportation mishandling can compromise packaging integrity, allowing contaminants to infiltrate. These issues endanger consumer safety and expose businesses to recalls, regulatory penalties, and reputational damage.
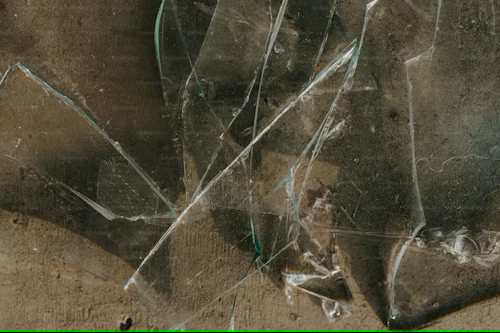
Limitations of Traditional Inspection Methods
Traditional methods like visual checks and metal detectors have significant limitations. Visual inspections are error-prone and ineffective for contaminants embedded in dense or opaque products. Metal detectors, while better, only identify metallic objects, missing non-metallic contaminants like plastic or stones. They also struggle with complex packaging, increasing the risk of undetected hazards and recalls.
The Growing Need for Advanced Detection Technologies
Consumers now demand safer products, and stricter regulations compel manufacturers to adopt better safety measures. Advanced technologies like food X-Ray machine offer a solution, capable of detecting a wide range of contaminants, including non-metallic materials and those hidden in multi-layered packaging. These systems ensure compliance with stringent standards, reduce recall risks, and help maintain consistent product quality. By adopting such innovations, businesses enhance their reputation for safety and reliability while staying competitive in the market.
How X-Ray Inspection Systems Prevent Contamination
Principles of Detection
X-Ray inspection for food industries operate on the principle of density differentiation. As X-Ray beams pass through products, they interact with internal structures, with denser materials like metals and glass absorbing more X-Rays and appearing darker in the resulting image. Advanced image processing software analyzes these variations in real time, flagging foreign objects that deviate from the expected density profile. Modern X-Ray inspection systems enhance accuracy using AI algorithms, adapting to diverse product types and improving detection capabilities over time.
Food X-Ray machine can detect a wide range of contaminants, including:
Metallic: Ferrous, non-ferrous metals, and stainless steel.
Non-Metallic: Glass shards, stones, ceramics, dense plastics, and rubber.
Organic: Bones from fish, poultry, or meat.
Miscellaneous: Sand, grit, and production debris like screws or washers.
Real-Time Detection and Rejection
Using high-resolution imaging, X-Ray inspection of food identify contaminants such as metals, glass, and dense plastics in real time. Automated rejection mechanisms, like air jets or mechanical arms, promptly remove defective items, ensuring only safe products reach consumers. This rapid process significantly reduces recall risks and protects brand reputation.
Multi-Material and Multi-Layer Detection and Non-destructive Detection
X-Ray inspection systems excel at detecting contaminants in complex products, including multi-layered or dense items. By analyzing density differences, they identify hidden contaminants within opaque packaging or intricate food combinations, ensuring thorough inspection across diverse product lines.
Enhancing Quality and Consistency
X-Ray inspection machine also verify product quality by identifying irregularities such as missing items, underfilled packages, or incorrect assemblies. For example, X-Ray food inspection ensure accurate counts and consistent sizes in food products like chocolates or cookies. This reduces waste and enhances consumer satisfaction by maintaining uniform production standards.
The Business Benefits of X-Ray Inspection
Reducing Recall Risks
X-Ray inspection systems minimize the risk of costly recalls by detecting contaminants like metal, glass, and plastic in real time. By removing defective products early, these food X-Ray machine prevent safety issues, reduce financial losses, and maintain production efficiency. Their ability to consistently ensure quality also reduces waste, making them a cost-effective safeguard for production lines.
Significantly Enhanced Detection Accuracy
X-ray inspection systems greatly enhance detection accuracy by leveraging density differentiation. X-rays penetrate products, highlighting internal structures based on density variations, allowing detection of foreign objects invisible to the naked eye. These systems can identify contaminants as small as 0.1mm, including metal fragments, glass, bones, stones, and dense plastics, even when embedded or obscured by packaging.
Increased Efficiency with Inline Detection
X-ray inspection systems are designed to seamlessly integrate into production lines, enabling real-time inline detection. Unlike offline inspection methods, which require manual handling and can disrupt workflow, inline X-ray systems operate continuously without interrupting production. For industries such as food production, where high throughput and rigorous quality standards are essential, the integration of X-ray inspection into production lines not only enhances efficiency but also boosts overall operational reliability and competitiveness.
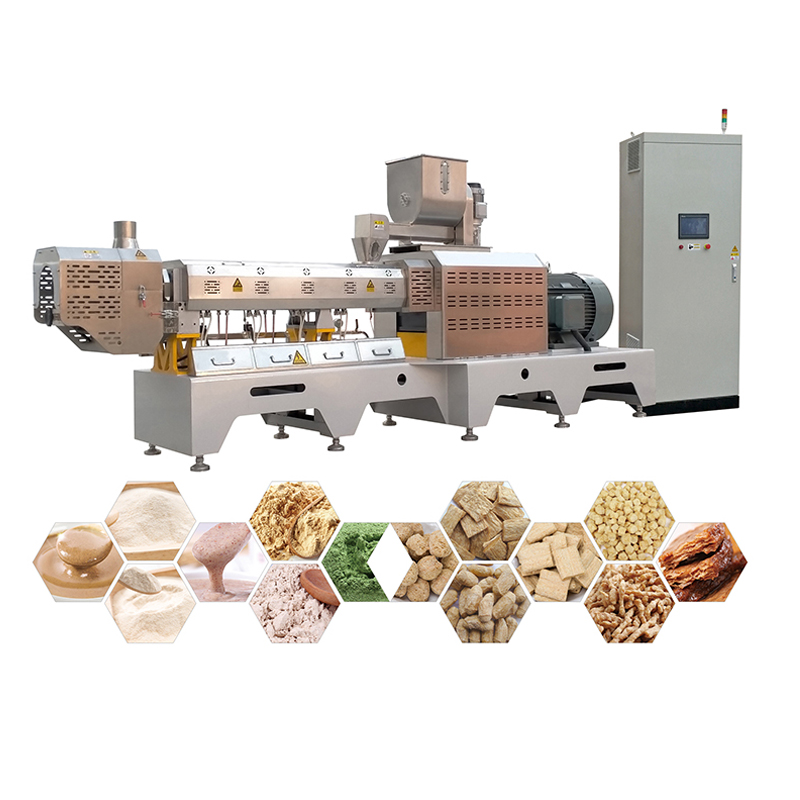
Ensuring Regulatory Compliance
X-Ray systems help manufacturers meet stringent global safety standards, including HACCP, FDA, and ISO certifications. By ensuring compliance with these regulations, these X-Ray inspection systems enable seamless operations and avoid penalties, particularly for businesses exporting to regions with diverse safety requirements.
Building Consumer Trust and Protecting Your Brand
Investing in X-Ray technology demonstrates a commitment to product safety and quality, building consumer trust and loyalty. A strong safety record protects brands from reputational damage while setting them apart in competitive markets, reinforcing their position as industry leaders.
Choosing the Right X-Ray Inspection System
Key Features to Look For
An effective X-Ray inspection system should include the following features to deliver reliable, accurate, and efficient results:
High Precision: Detection accuracy is essential to identify contaminants of various shapes, sizes, and densities. Foodman X-Ray inspection machine utilize advanced imaging technology that provides exceptional resolution, enabling the detection of even the smallest foreign objects.
AI Algorithms: AI capabilities are a game-changer in food inspection. Foodman X-Ray inspection equipment are equipped with FIAP (Foodman Intelligent Algorithm Platform), which uses deep learning and large-scale image analysis to enhance detection accuracy, minimize false positives, and continuously improve performance.
Real-Time Monitoring: Foodman X-Ray inspetcion systems feature real-time data analysis, allowing for immediate detection and removal of defective products. This ensures uninterrupted production and helps maintain efficiency on high-speed lines.
Multi-Material Detection: A robust X-Ray system should detect a wide range of contaminants, including metals, glass, stones, bones, and dense plastics. Foodman X-Ray systems excel in identifying contaminants across diverse product types, from solid items to liquids, packaged products, and multi-layered goods.
Environmental Adaptability: Foodman systems are designed to operate under challenging conditions, such as high humidity or extreme temperatures, without compromising performance.
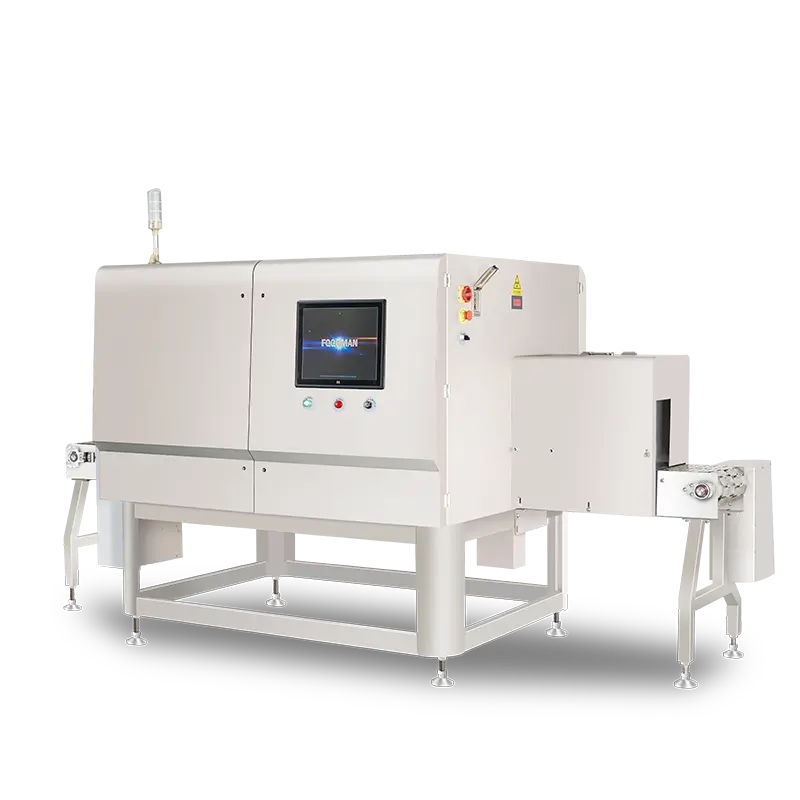
Tailoring Solutions for Your Business
With over 15 years of expertise in food inspection technology, Foodman has established itself as a leader in advanced X-Ray solutions. The X-Ray inspection machine are designed to help manufacturers meet global safety standards, including HACCP, FDA, and ISO certifications. By choosing Foodman, you’ re investing in precision, innovation, and the confidence that your products meet the highest quality and safety standards.
Foodman X-Ray Inspection Systems not only prevent costly recalls and ensure regulatory compliance but also enhance operational efficiency and build consumer trust. Tailored to meet the demands of diverse industries, Foodman is your trusted partner for safeguarding your brand and delivering excellence.
Conclusion
Reinforcing the ROI of X-Ray Inspection System
Investing in X-Ray inspection systems is a strategic move that ensures food safety while delivering measurable returns. By detecting contaminants early, these systems minimize waste, prevent costly recalls, and maintain consistent product quality, protecting both financial stability and brand reputation.
X-Ray inspection also helps manufacturers comply with strict global food safety regulations, avoiding fines and operational disruptions. Automating inspections reduces human error and boosts efficiency. Though the initial cost may seem high, the long-term benefits—avoided recalls, reduced waste, and increased customer loyalty—make it a sound investment.
Take the First Step Toward Safer Products
Adopting X-Ray technology is a proactive commitment to safety, quality, and consumer trust. These X-Ray systems for food industry empower manufacturers to meet growing consumer expectations for safe, high-quality products while identifying and eliminating potential risks.
Don’ t wait for recalls or safety breaches to act. Investing in X-Ray inspection systems today secures your brand’s reputation and ensures a safer production process. Take the first step toward a safer, more reliable future now.