Ensuring Dairy Product Safety: Challenges, Contaminants, and the Role of X-Ray Inspection
The Importance of Quality and Safety in the Dairy Industry
Dairy products are an essential part of the global food supply, but maintaining their safety and quality is a constant challenge. Contamination, spoilage, and packaging defects can pose serious health risks to consumers and lead to costly recalls for manufacturers. To meet stringent food safety regulations and ensure product integrity, advanced inspection solutions are necessary. This is where food X-Ray inspection equipment plays a crucial role.
Common Contaminants and Defects in Dairy Products
Dairy products, including milk, cheese, yogurt, and butter, are susceptible to various contaminants. These can include:
Foreign objects such as metal fragments, glass shards, and plastic pieces.
Bone fragments in dairy-based meat products.
Packaging defects, such as air bubbles in cheese or improperly sealed containers.
Product inconsistencies, like missing portions or incorrect filling levels.
Traditional inspection methods often fail to detect low-density contaminants, but X-Ray machines for food inspection provide a more reliable solution.
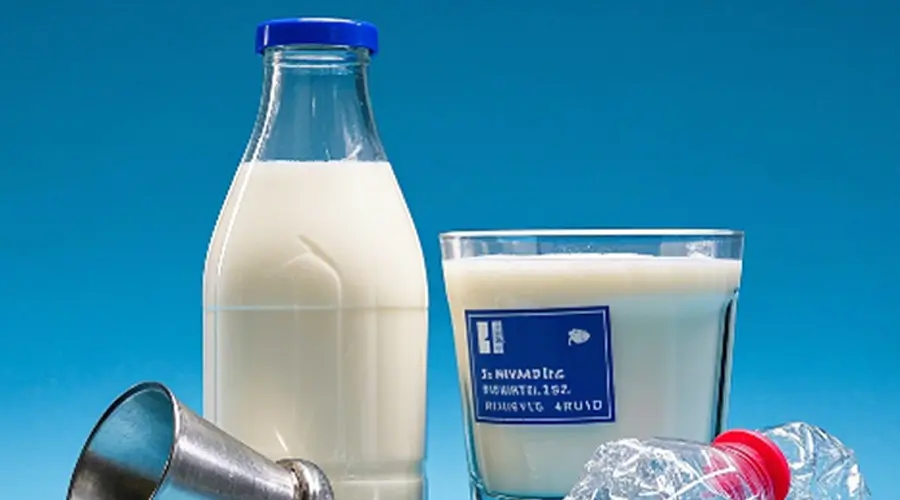
How X-Ray Inspection Enhances Food Safety and Compliance
Modern X-Ray inspection machines offer a non-destructive and highly accurate way to ensure dairy product safety. These X-Ray machines for food processing detect even the smallest contaminants, improving overall quality control. Key benefits include:
Comprehensive contaminant detection: Unlike metal detectors, food X-Ray inspection systems can identify a wide range of foreign objects, including glass, stone, and dense plastics.
Automated quality control: X-Ray inspection machines streamline production by automatically detecting and rejecting defective products.
Regulatory compliance: Using X-Ray inspection ensures compliance with global food safety standards, helping dairy manufacturers meet HACCP, FDA, and other regulatory requirements.
By integrating X-Ray inspection systems, dairy producers can safeguard their products, protect consumers, and enhance operational efficiency. As food safety standards continue to evolve, food X-Ray inspection equipment remains a critical investment for the dairy industry.
Challenges in Dairy Product Safety & Quality Control
Ensuring the safety and quality of dairy products is a top priority for manufacturers. However, various challenges—ranging from foreign body contamination to regulatory compliance—demand advanced inspection solutions. Food X-Ray inspection equipment plays a crucial role in addressing these challenges, improving product integrity, and safeguarding consumer health.
Potential Foreign Body Contamination (Metal, Glass, Plastic, etc.)
Dairy production environments involve multiple processing stages, increasing the risk of foreign contaminants. Metal fragments from machinery, glass shards from packaging, and plastic particles from processing materials can compromise product safety. X-Ray machines for food inspection offer a reliable way to detect and remove these hazards, ensuring consumer protection and regulatory compliance.
Variability in Product Density and Packaging Materials
Dairy products come in various forms—liquids, solids, and semi-solids—each with unique density and packaging requirements. Traditional detection methods often struggle with inconsistencies in density, but X-Ray inspection machines can accurately analyze different products and packaging materials, maintaining high-quality standards.
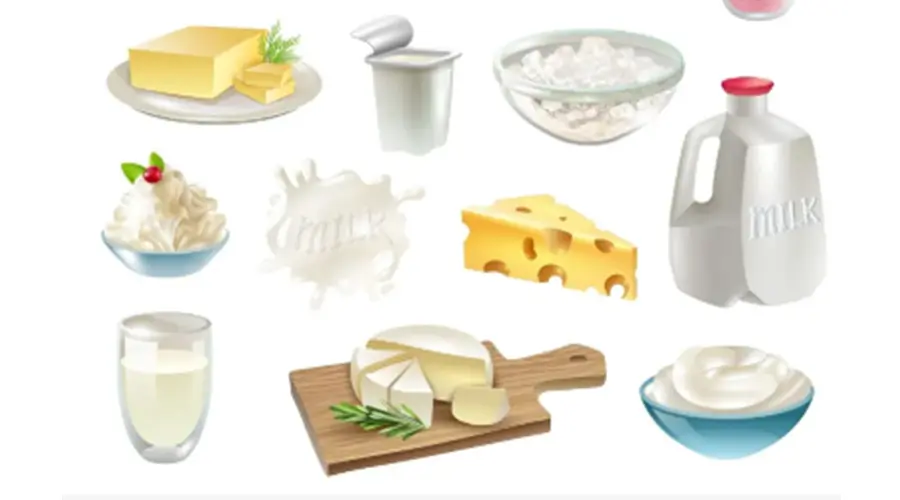
Risks of Underfilled or Overfilled Products
Accurate filling is crucial for dairy manufacturers to meet weight regulations and avoid consumer complaints. Overfilled products lead to waste, while underfilled items can violate industry standards. X-Ray machines for food processing help monitor fill levels in real time, ensuring each product meets precise volume requirements.
Ensuring Compliance with Food Safety Regulations (FDA, HACCP, etc.)
Strict food safety regulations, such as FDA and HACCP guidelines, require manufacturers to implement robust quality control measures. Food X-Ray inspection technology helps dairy producers meet these regulations by providing detailed contamination analysis and automated rejection of non-compliant products.
By integrating X-Ray inspection systems, dairy manufacturers can overcome safety and quality challenges, reduce waste, and maintain consumer trust. Investing in food X-Ray inspection equipment is an essential step toward achieving higher standards in dairy product safety and quality control.
How X-Ray Inspection Works in Dairy Processing
Maintaining the highest standards of safety and quality in dairy products is essential for manufacturers. Food X-Ray inspection provides an advanced, non-destructive solution for detecting contaminants, ensuring proper fill levels, and identifying packaging defects. Let’s explore how X-Ray inspection machines enhance dairy processing.
Detecting Foreign Contaminants in Liquid and Solid Dairy Products
Contamination in dairy products can occur due to metal, glass, plastic, or other foreign materials introduced during processing. X-Ray machines for food inspection can detect these contaminants even in thick or opaque packaging, ensuring that milk, cheese, yogurt, and other dairy items meet safety standards. Unlike traditional metal detectors, food X-Ray inspection equipment can identify a wider range of foreign objects, including non-metallic materials.
Ensuring Proper Fill Levels in Milk Cartons, Yogurt Cups, and Cheese Packages
Accurate fill levels are crucial for both regulatory compliance and customer satisfaction. X-Ray machines for food processing allow manufacturers to monitor and verify the correct volume of liquid and solid dairy products in sealed packaging. By preventing underfilling or overfilling, X-Ray inspection systems help reduce waste and optimize production efficiency.
Identifying Packaging Defects Such as Leaks, Seal Integrity Issues, and Missing Components
Packaging defects can lead to product spoilage, contamination, and customer dissatisfaction. X-Ray inspection machines can detect issues such as leaks, seal integrity failures, and missing components in dairy packaging. This ensures that products maintain freshness and comply with strict food safety regulations.
By integrating food X-Ray inspection technology into dairy processing, manufacturers can achieve greater safety, efficiency, and compliance. Investing in X-Ray inspection systems helps ensure that dairy products reach consumers in the best possible condition, free from contaminants and defects.
Advantages of X-Ray Inspection for Dairy Products
Ensuring the safety and quality of dairy products requires advanced inspection technology. Food X-Ray inspection has become an essential tool in modern dairy processing, offering superior contaminant detection, packaging inspection, and production efficiency. Here’s why X-Ray inspection machines are a game-changer for the dairy industry.
Superior Detection Capabilities Compared to Traditional Metal Detectors
While metal detectors are commonly used in food processing, they are limited to detecting only metallic contaminants. X-Ray machines for food inspection go beyond metal detection, identifying foreign objects like glass, plastic, rubber, and even tiny bone fragments in dairy products. This ensures a higher level of food safety and compliance with strict regulations.
Non-Destructive Inspection That Preserves Product Integrity
Unlike other inspection methods that may require product destruction for quality checks, food X-Ray inspection equipment provides a non-invasive solution. Whether inspecting milk, cheese, yogurt, or butter, X-Ray inspection machines analyze products without compromising their integrity, allowing manufacturers to maintain product quality while ensuring safety.
Ability to Inspect Products in Various Packaging Types (Plastic, Foil, Glass, Etc.)
Dairy products are packaged in a variety of materials, including plastic containers, foil-sealed cups, glass bottles, and cartons. X-Ray machines for food processing effectively scan through different packaging types without interference, making them a versatile solution for comprehensive food safety checks.
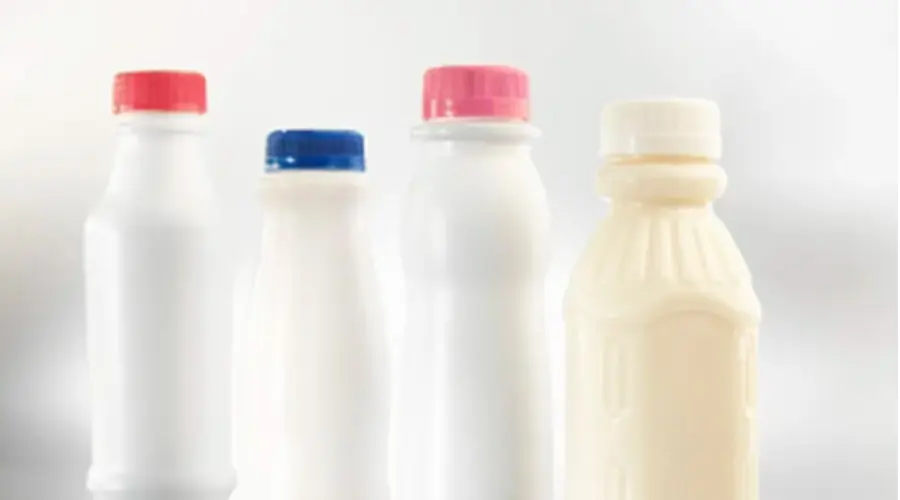
High-Speed Inspection for Continuous Production Lines
To keep up with the high demands of dairy production, X-Ray inspection systems offer rapid and automated inspections without slowing down the production line. This ensures efficiency while reducing the risk of recalls, rework, and waste.
By incorporating X-Ray inspection machines into dairy processing, manufacturers can achieve a higher standard of food safety, product quality, and operational efficiency. Investing in food X-Ray inspection technology is a proactive step toward ensuring consumer confidence and regulatory compliance in the dairy industry.
Meeting Industry Standards & Consumer Expectations in Dairy Processing
Ensuring the safety and quality of dairy products is a top priority for manufacturers. Compliance with strict food safety regulations and maintaining consumer trust require advanced inspection solutions. Food X-Ray inspection plays a crucial role in meeting industry standards while preventing costly recalls and protecting brand reputation.
Compliance with Food Safety Regulations (FDA, USDA, BRC, etc.)
Regulatory bodies such as the FDA, USDA, and BRC enforce strict guidelines to ensure food safety in dairy processing. X-Ray inspection machines help manufacturers comply with these regulations by detecting foreign contaminants, verifying product integrity, and ensuring proper packaging. By integrating X-Ray machines for food inspection, dairy producers can maintain compliance while enhancing overall quality control.
Reducing Product Recalls and Brand Reputation Damage
A single contaminated product can lead to costly recalls and severe damage to a brand’s reputation. Food X-Ray inspection equipment provides an advanced detection system that helps prevent such incidents by identifying contaminants like metal, glass, and plastic before products reach consumers. Early detection reduces waste, minimizes financial losses, and safeguards brand integrity.
Enhancing Consumer Confidence in Dairy Product Quality
Consumers expect dairy products to be safe, fresh, and free from contaminants. Implementing X-Ray machines for food processing ensures a higher level of quality assurance, reinforcing consumer trust. By using cutting-edge X-Ray inspection systems, dairy manufacturers can demonstrate their commitment to safety, boosting customer confidence and brand loyalty.
Investing in X-Ray inspection is more than just meeting regulations—it’s about delivering safe, high-quality products that consumers can trust. With X-Ray inspection machines, dairy processors can uphold the highest food safety standards while ensuring efficiency and reliability in production.
Future Trends in X-Ray Inspection for the Dairy Industry
As technology advances, X-Ray inspection in the dairy industry is evolving to improve accuracy, efficiency, and sustainability. Modern food X-Ray inspection equipment is integrating AI, smart manufacturing, and sustainability initiatives to enhance food safety while optimizing production.
AI-Powered Detection for Increased Accuracy and Efficiency
Artificial intelligence (AI) is transforming X-Ray inspection machines by improving contaminant detection and reducing false rejects. AI-driven food X-Ray inspection systems can analyze vast amounts of data, learning to differentiate between actual contaminants and harmless variations in dairy products. This leads to more precise inspections, fewer product losses, and increased efficiency in X-Ray machines for food processing.
Integration with Industry 4.0 and Smart Manufacturing
The adoption of Industry 4.0 technologies is revolutionizing X-Ray machines for food inspection by enabling real-time monitoring, automated adjustments, and predictive maintenance. Connected X-Ray inspection systems can seamlessly integrate with smart production lines, providing manufacturers with valuable insights into product quality and process efficiency. This level of automation enhances food safety while reducing operational costs.
Sustainability Initiatives: Reducing Waste and Improving Production Efficiency
Sustainability is a growing focus in the dairy industry, and X-Ray inspection machines are playing a role in minimizing waste. By detecting foreign objects, incorrect fill levels, and packaging defects early, food X-Ray inspection equipment helps prevent unnecessary waste of dairy products. Additionally, more energy-efficient X-Ray machines for food processing contribute to overall sustainability efforts by optimizing resource use and reducing environmental impact.
The future of X-Ray inspection in the dairy industry lies in smarter, faster, and more sustainable solutions. By embracing AI, Industry 4.0 integration, and eco-friendly innovations, dairy manufacturers can improve food safety, efficiency, and compliance while staying ahead in an evolving market.
Conclusion
The Critical Role of X-Ray Inspection in Ensuring Dairy Product Safety and Purity
In the dairy industry, maintaining high standards of safety and quality is essential. X-Ray inspection plays a vital role in detecting foreign contaminants, ensuring product integrity, and verifying packaging quality. With the increasing complexity of production processes, food X-Ray inspection equipment has become indispensable for manufacturers striving to deliver safe and pure dairy products to consumers.
Why Dairy Manufacturers Should Invest in Advanced Inspection Technology
Investing in X-Ray machines for food inspection provides numerous benefits, including superior detection capabilities compared to traditional methods like metal detectors. Modern X-Ray inspection machines can identify contaminants such as glass, plastic, and rubber while also detecting inconsistencies in product weight, shape, and fill levels. Advanced X-Ray machines for food processing enable dairy manufacturers to maintain consistent quality and comply with stringent food safety regulations.
Encouraging Industry Adoption of X-Ray Inspection for Better Quality Assurance
To meet growing consumer expectations and regulatory requirements, more dairy manufacturers should integrate X-Ray inspection systems into their quality control processes. By adopting food X-Ray inspection technology, companies can reduce product recalls, protect brand reputation, and enhance overall production efficiency. The future of dairy safety relies on advanced inspection solutions that ensure purity, compliance, and consumer confidence.